Systems Engineering, the journal of The International Council on Systems Engineering (INCOSE) has published my most recent paper, entitled “A systems-engineering approach to nation-scale problems: Municipal solid waste management in Saudi Arabia“.
Paper Overview (TL;DR)
We applied systems-engineering techniques to investigate how municipal solid waste (MSW) is treated, using Saudi Arabia as a case study. We built a mathematical model of the system and used it to investigate different scenarios.
This model showed that a combination of anaerobic digestion (for food and organic waste), recycling and incineration (for non-recyclable materials) would reduce the total mass of waste to landfill by 73%. Not only that, this approach reduced the effect of the waste management on the environment by 98%.
Motivation
In Saudi Arabia, municipal solid waste (MSW) is currently disposed of in landfill (dumping it in a hole). This causes irreparable environmental harm and increased hazard from the possibility of landfill fires.
However, the Saudi MSW system is a large, multi-stakeholder (lots of people are interested in the outcome) system. This makes it a great system to develop “nation-scale” (really big) systems engineering tools on.
System Model
My previous work has focussed on modelling rail vehicles and infrastructure, and using these models to investigate how to reduce their emissions. So we took that and applied it to this giant system – the Saudi MSW system:
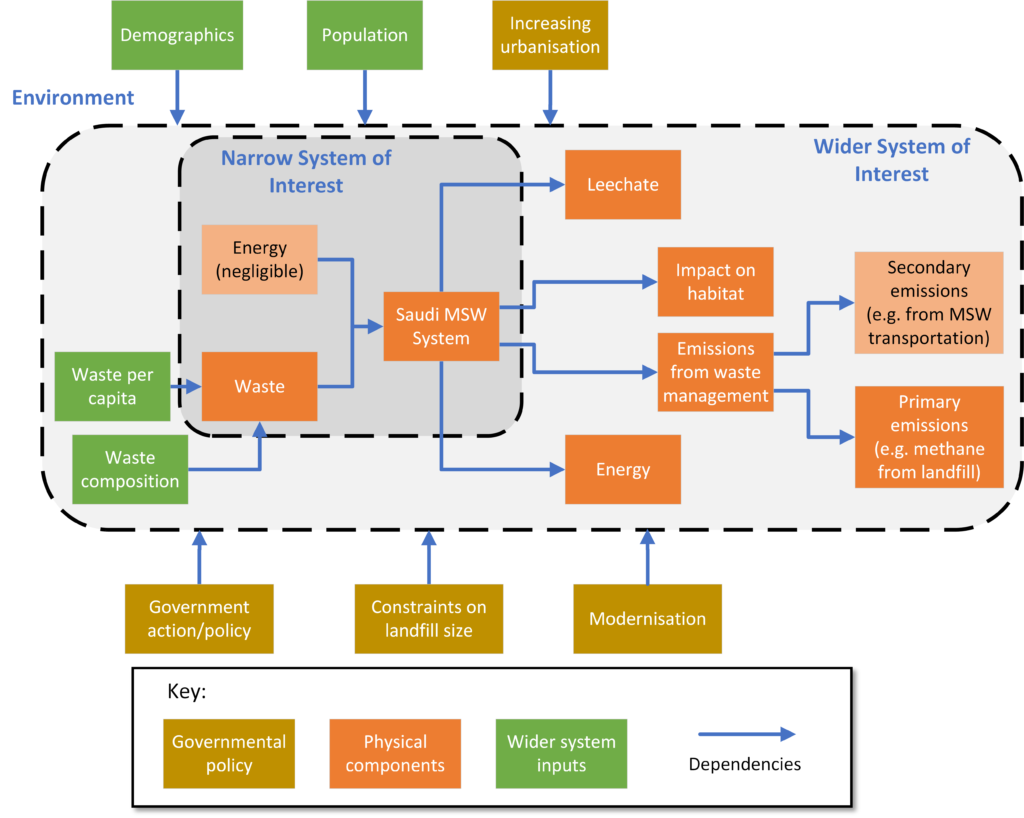
Then we built a mathematical model of the system, so that we could understand how the narrow system of interest (the waste stream) behaved when we changed some of the inputs. (This involved lots of checking through other people’s work to see how these things should be modelled!) Finally, we came up with a (pretty complex!) system model that looked like this:
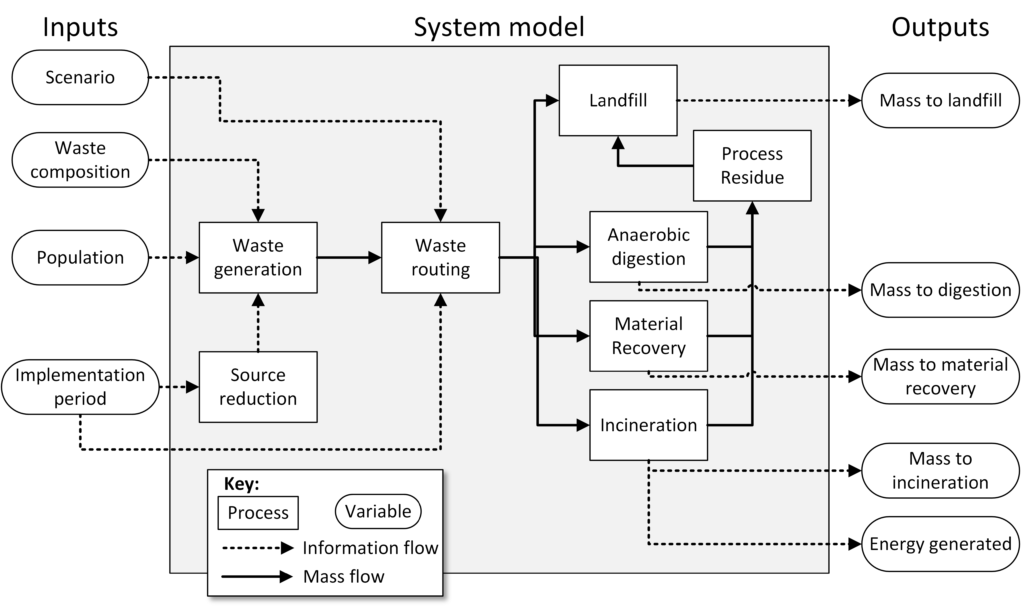
Then, we made some assumptions about about the makeup of the waste, and the likely population growth over the next 30 years. With that done, we could then answer two basic questions: What happens if we do nothing? What happens if Saudi citizens reduce their waste per person from 1.38kg/day to 1.14kg/day (in line with the UK)? And the answer is:
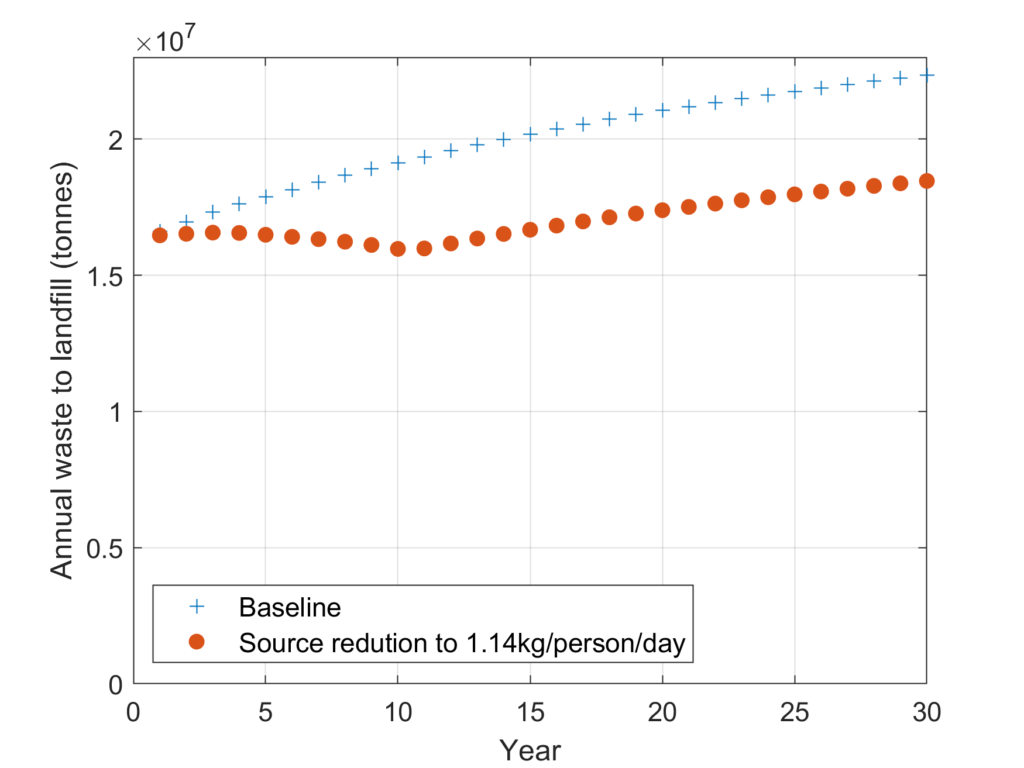
Using the Model
Then, we took this freshly made model and applied it to a range of possible scenarios that we’d devised, based on what we would do, and what other people had suggested:
Scenario number | What it involved |
Scenario 0 (baseline) | Everything to landfill |
Scenario 0.1 | Everything to landfill, but less waste per person (1.14 kg/person/day) |
Scenario 0.2 | Everything to landfill with much less waste per person (1.02 kg/person/day) |
Scenario 1 | Food, glass and metal to landfill. Everything else is incinerated |
Scenario 2 | Everything except glass and metal goes to anaerobic digestion |
Scenario 3 | Anaerobic digestion or recycling for everything. (Incineration for textiles) |
Scenario 4 | Anaerobic digestion or recycling for everything. (Landfill for textiles) |
And this gave us some pretty graphs, showing how much waste went to landfill in each year for each of the scenarios. (Each of the measures was given 10 years to implement, because making new infrastructure takes time.)
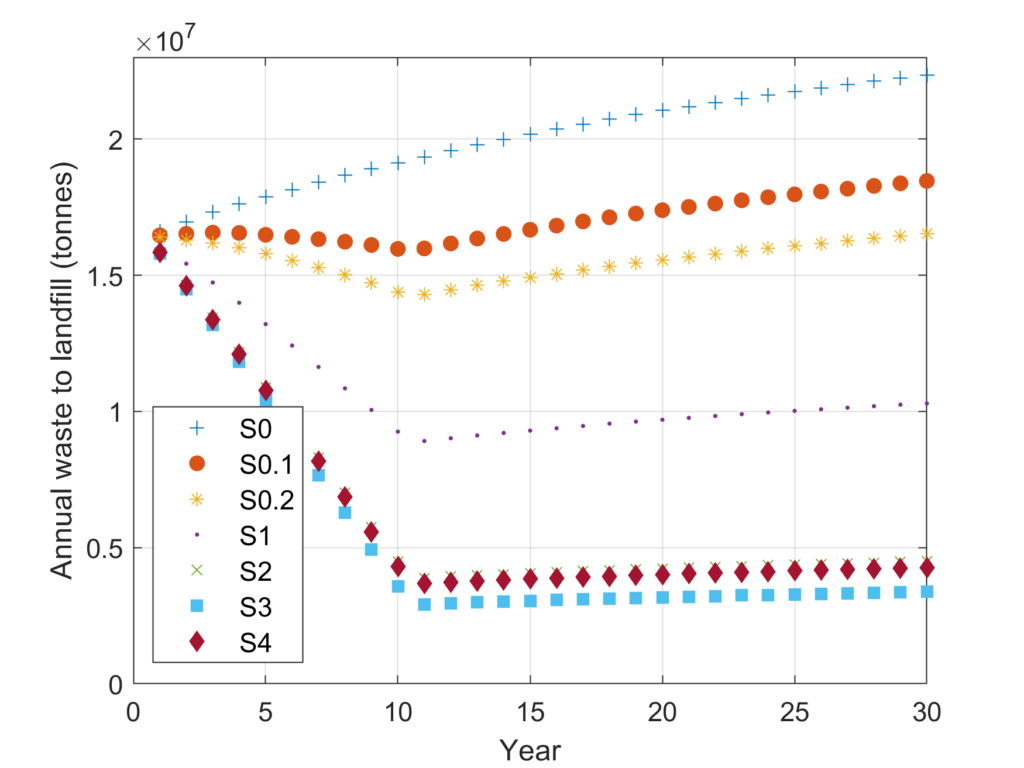
Then, we could look at how much went to landfill in total over the 30-year horizon of the simulation:
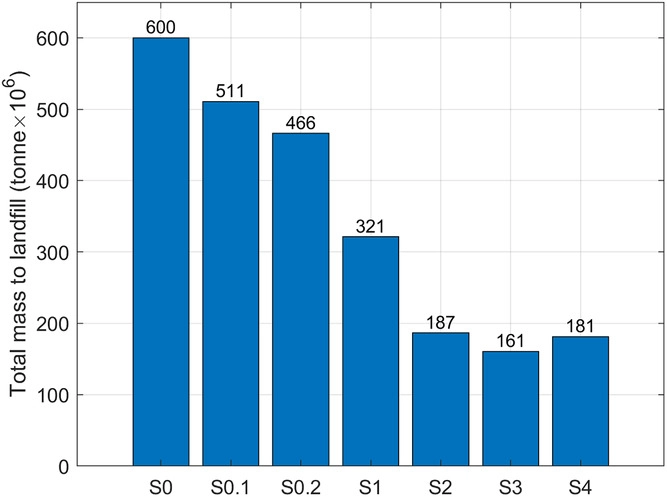
This is pretty clear! S3 leads to the lowest total mass to landfill over the 30 years of the study. Job done!
Environmental Impact
Well, almost. Finally, we wanted to check how the environmental effects of each of the scenarios compared. For this we used a commercial life cycle analysis (LCA) tool called SimaPro. We modelled each of the scenarios in this tool, and compared the DALY for each of them. (DALY stands for disability-adjusted life year, or how much of an effect a certain action has on people’s lives. The higher the number, the worse the effect on us.)
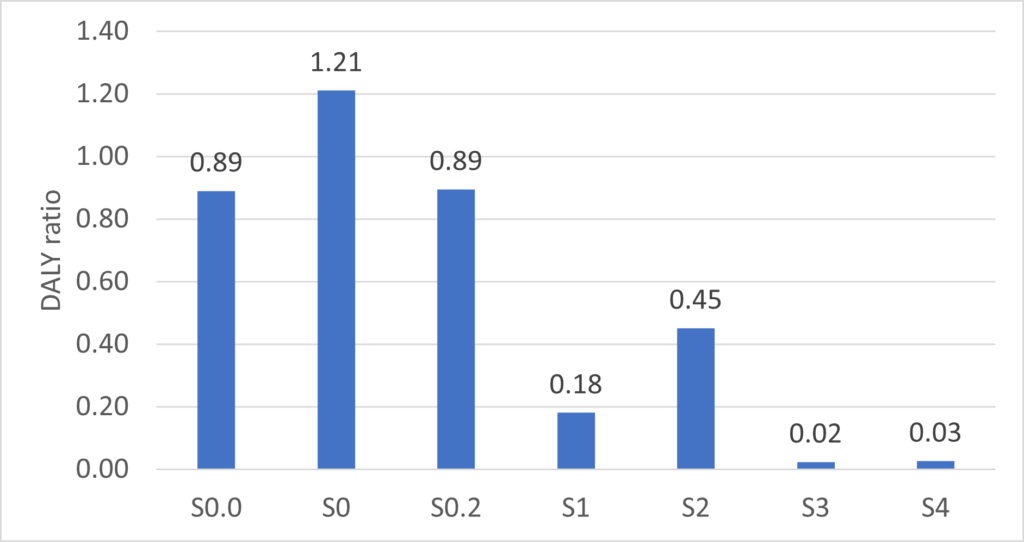
You can see that all of the changes suggested by our systems engineering for waste management study have reduced the hazard the waste poses to people’s lives. In fact, Scenario 3 has only 2% of the impact on people’s lives of the current system. This is encouraging!
Conclusions
The results of this study into systems engineering for waste management are encouraging!
- Just reducing the amount of waste people create would reduce the amount of waste to landfill by 89 million tonnes over 30 years.
- Scenario 3 (anaerobic digestion of most waste, combined with recycling and limited incineration of non-recyclable materials) is the winner! This would save 328 million tonnes of waste going to landfill over the next 30 years.
- Scenario 3 also reduces the impact of waste management on people’s health by 98% compared to the current system.
Other work
For more information on my research, please check out my Research page.